EXISTING CONDITION:
The existing mechanical systems were 50’s vintage water and steam boilers and air handlers, with pneumatic (air powered) controls. With many of the controls not operating there was no outside air economizer or any other modern controls in place to control efficiency and temperatures.
Employees were running to the basement during dining hours and manually turning on and off the boilers and air conditioning.
Wireless Automation Added to Building
With all the controls running on air, there was no way to automate or change the operational parameters to a modern energy management system. A wireless automation system was added to control heating, cooling, economizing and scheduling. The system could then offer real-time data and can be controlled or viewed by any internet connection and on any smart phone.
Steam Heat in Air Handlers Converted to Water
Two air handlers were being used for cooling, fresh air and booster heat. The steam system was converted to heat water and utilized one of the two boilers that had excess capacity. A balancing automated valve was used to divert boiler water to the air handlers when need for booster heat.
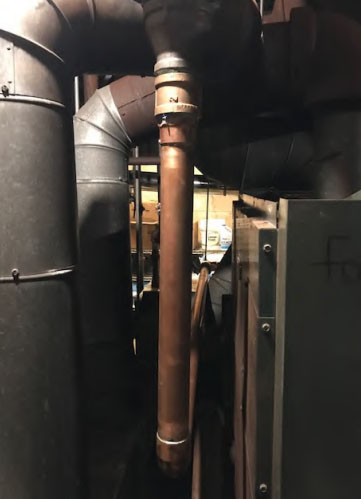
Kitchen MUA Converted from Steam to Electric
The existing MUA had a 1.4 MMBTU steam boiler that only worked intermittently but had to run for at least 15 minutes just to make steam. The steam was also used as a booster system for warm up in the restaurant but again was used only intermittently. When the boiler broke down and was in need of replacement, it was determined that the other two water boilers could be used for the booster system, and the kitchen system could have a inline duct heater. Since this heater is only used to temper the MUA., the energy usage was minimum.
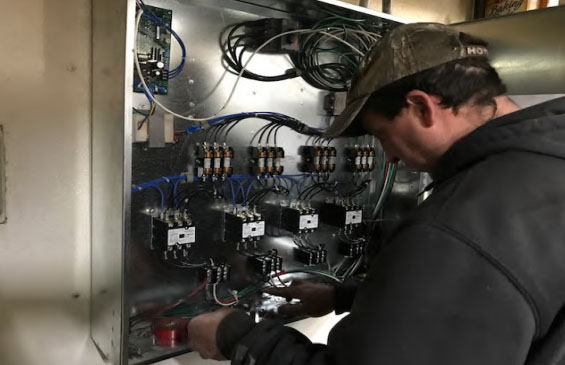
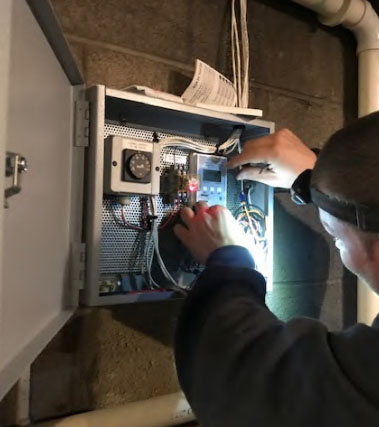
PROJECTED SAVINGS
$6,333
Your Content Goes Here
New Electric Damper Motors Added to Control Outside Air
The existing dampers hadn’t operated in years and were stuck in a closed position. The dampers were loosened up and new actuators were added to control the outside air and balance the incoming air to mitigate temperature extremes. This now allows for full economizing instead of mechanical cooling that was being used even in winter when the dining room filled up with customers.
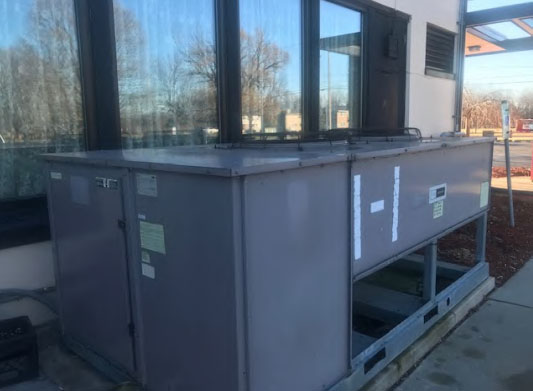
Mechanical cooling is now controlled by the new automation system
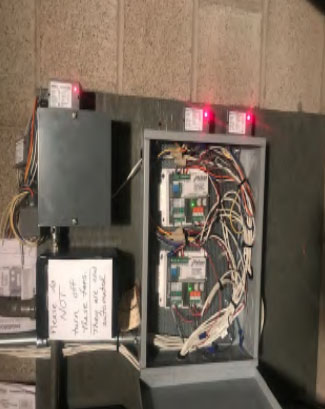
Pelican Automation was used to replace the pneumatics
Custom Controls
Tower developed a control system that took over the old steam heating valves by intercepting the air signal from the pneumatics and having it respond to a modern control signal. Additional relays were added to control the 40 ton cooling system and work with the new economizer. The new system was integrated into the Tekmar boiler controls so that the boiler was disabled when the restaurant was calling for cooling. It is very common for the facility to need cooling when fully occupied, even in winter, so having the heat running during a call for cooling made both the heating and cooling run at full capacity when not needed.
This new control is expected to save 40% on total energy costs throughout the season.
Additional Boiler Outside Air Reset and Control
The boilers had no temp control of the loop temp and were being manually raised and lowered to accommodate outside air temperatures. A new control system was added to raise and lower boiler circulation loop temperatures automatically and disable the system when outside air temperatures reached 55F. This saves energy and cuts costs on heating throughout the season.
Real-Time Monitoring and Control
Real-time monitoring and controls spot problems in the mechanicals during normal hours and prevent emergency calls at night and weekends.
Spotting problems early also prevent breakdowns and expensive repairs.
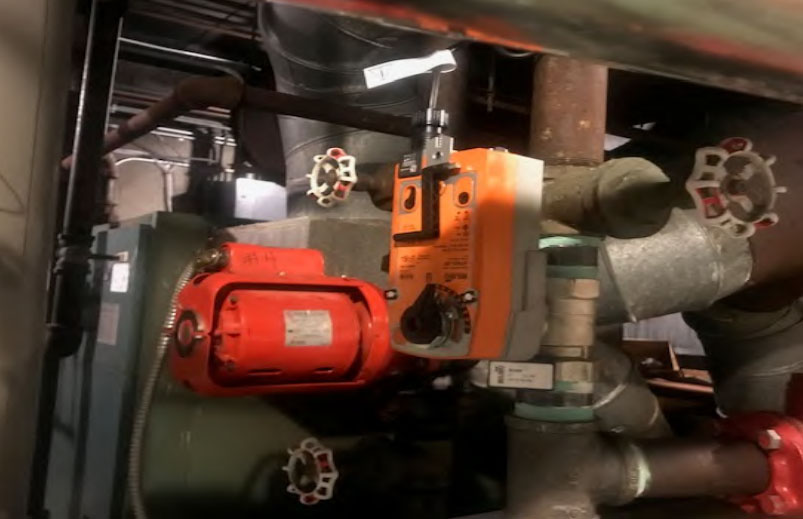
Balancing valves were added to the circulation loop to allow use of the same boilers for booster heat – eliminating the need for a separate steam
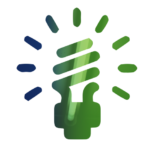
REAL-TIME MONITORING AND CONTROLS
Real-time monitoring and controls spot problems in the BAS and plant operations based on energy usage not just performance. Usage spikes out of the norm indicate equipment or control malfunctions long before they would normally show up on the utility bill. Other issues concerning parts failure are also spotted in advance preventing costly maintenance.
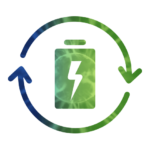
CUSTOM CONTROLS
Tower developed a control strategy that didn’t interfere with the existing oxidizer operation and maintained discharge air pressures through the stack. Safety issues were also integrated for fire and low discharge air temps to prevent the system from cooling in the event of oxidizer shit down or failure. Additional integration allows visibility through the existing new BAS and provided data for temps throughout the plant and heating control of the MUA units. The MUA units were controlled also to maintain slightly negative building pressure in the areas served. This allowed the units to fully take advantage of the MUA provided by the new system and modulate down based on building pressure.
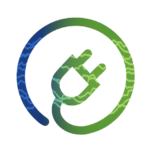
TOWER ENERGY MECHANICAL
Licensed mechanical contractors with 30+ years of experience. Licensed master electricians specializing on controls. Practical customized engineering experience to spot opportunities and estimate payback and costs.