EXISTING CONDITION:
The existing mechanical systems were standard McDonalds specifications, which controlled building pressures with use of economizers in the RTU’s. There is substantial fixed speed exhaust to mitigate however while trying to maintain comfort. All controls were centrally located in the office for the RTU’s and were routinely overridden by managers.
Central Wireless Automation System was Added to the Existing Mechanicals
Four RTU’s ranging from 6-12.5 tons were integrated into a central wireless control system to manage temperatures remotely and standardize set points. This took local control away from the employees and set the stores to corporate standards. All schedules were also standardized to not allow overrides.
Economizer Advanced Controls Added
All economizers were taken over with new controls that maximize use of OA while not over ventilating. DCV (demand control ventilation) utilizes sensors to read CO2 in the air and add OA when needed to maintain proper air quality. The same system is used to prevent unnecessary ventilation.
Kitchen System Modified to Maximize Air Make-up
The kitchen unit previously was set to 68F during summer and winter, which ended up using mechanical cooling 365- 24/7 since the area could not meet 68F due to the heat generated in the area. After testing the system, we reset the area settings to 76F and integrated a OA mechanical cooling cut-off to 50F to prevent mechanical cooling and utilize OA to fully ventilate as much as possible.
Electric Window Heat Controlled with Same System
Window ceiling electric booster heat were operating uncontrolled and were routinely set to 85F. We found these systems operating while the mechanical cooling was also operating in the kitchens. The thermostat was also not on a schedule, so it was also running all night when they were closed. Tower added a control relay to the new control system and set the temperature to operate only when needed.
Electrical Saving on Building Automation– 20 hr/day Average Store
Unit | Yearly Savings | Cost Savings |
---|---|---|
Kwh | 90,080 | $ 8,799.00 |
Maintenance | 40% | $ 12,995 |
10 yr Savings
$ 94,155.93
Elimination of service calls
Actual ROI
Reduced Service Calls
The remote real-time data on how each RTU is operating gives a better perspective on equipment operation and eliminates 40% of service calls by average. Data is compiled in real time and can spot operational problems early to prevent emergency failures.
Aging & Inefficient Store lighting
Store lighting was aging and inefficient. The old system was removed and replaced with an efficient LED system that can be cleaned easily and has no hazardous components for maintenance.
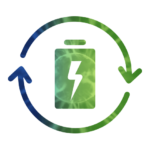
TOWER ENERGY CAN CHANGE YOUR ENERGY BILL
Using new and innovative technologies, Tower Energy can reduce your gas, electric and water bills. Looking for practical and less expensive alternatives using existing equipment is always a viable option. In addition, making employees aware of simple fixes will add operational efficiency at little or no cost.
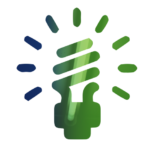
UTILITY SUBSIDY AND GRANT PROCUREMENT
Tower Energy finds We-Energy grants to subsidize most projects.
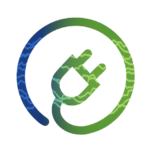
FREE ENERGY ASSESSMENT AND TAX ANALYSIS
Tower Energy will conduct a free energy assessment to evaluate opportunities that may exist. We also analyze your utility bills for exemptions from The EPA Energy Act of 2006. This frequently results in a tax refund or exemption on energy used in your facility.