EXISTING CONDITION:
After a major energy upgrade that included a heat pipe, DCV (Demand Control Ventilation), economizer with entropy, BAS control with advanced analytic and lighting savings that was being tracked, the entire system of tracking individual systems was deteriorating.
During this time, real-time monitoring and control was lost.
THIS 60,000 SQ.FT. FACILITY WAS LEED CERTIFIED WITH ENERGY SAVING TECHNOLOGY
Before starting the project, the building had a modern energy management system in place with VFD’s on the drive and supply motors along with VAV’s in all rooms. The drives, however, were only balancing static pressure in the ducts. The air was being over cooled for de-humidification and being reheated at the AHU.
HEAT PIPE ADDED TO EVAPORATOR COILS TO ACHIEVE REHEAT
To eliminate the costly reheat, a heat pipe was added in front of and behind the evaporator coils to both pre-cool and pre-heat the air coming from the return and outside air intake. This technology transfers heat from the return side to the supply side via a change in state of the gas in the coil. This is done without pumps or motors and will save an equal amount of cooling energy since the additional cooling does not have to be done to overcome the differential. Altogether, this saved 46 tons of cooling.
BAS REPROGRAMMED TO MAXIMIZED UTILIZATION OF VFDS ON STATIC PRESSURE
The entire VAV air flow settings were customized so that each area had it’s own flow that matched actual demand. Stock settings from the factory have no relevance to actual occupancy. VAV “tuning” involves monitoring and control to spot variances off set-point during seasonal changes. It can take 18 months to tune the system properly and maximize savings. This allowed the 80 hp of supply and return motors to modulate to 35-45hz and save between 50-80% of electrical energy to run the system.
THERMS PER MONTH BASED ON RECOVERY ALONE
DATE | 2014 | 2015-16 | SAVINGS |
---|---|---|---|
9/22/16 | 2,454 | 1579 | $ 649 – lost control |
10/22/16 | 3,689 | 706 | $ 2,207 – w/control |
11/22/16 | 3,930 | 1,000 | $ 2,168 – w/control |
TWO MONTH ADDED SAVINGS WITH CONTROL
$ 4,375
Supply And Return Pressure Settings Changed To Increase Flow
Standard supply settings were 20% over return, which was restricting flow and causing back pressure in the rooms. To correct this, Tower Energy increased return speeds 3% higher than the supply, which quieted the building and improved return flows substantially. This also allowed for lower general static pressures and fan speeds for the entire facility.
KWH SAVINGS FROM CHANGES AFTER MONITOR AND CONTROL WAS REGAINED
DATE |
2013 |
2015-16 |
SAVINGS / MONTH |
---|---|---|---|
7/19/16 | 164,170 | 153,300 | $ 1,285 – lost control |
8/19/16 | 152,310 | 175,350 | $ -2,999 – no control |
9/19/16 | 156,570 | 133,320 | $ 2,909 – w/control |
10/19/16 | 143,670 | 98,370 | $ 5,898 – w/control |
11/19/16 | 105,900 | 80,370 | $ 3,324 – w/control |
12/19/16 | 107,730 | 78,810 | $ 3,765 – w/control |
SAVINGS WITH CONTROL
$ 15,896
Months Payback after Grants
Projected Return on Investment
One Year Projected Savings
MECHANICAL PROBLEMS SPOTTED
After 36 months of operation, a dramatic rise in therm usage and electrical costs were noticed, which required investigation. Although the summer temperatures where a lot higher than average, the spike in energy use was not expected and was higher prior to all the improvements. Real-time monitoring was not available for these months, and when it was regained, we immediately realized the boiler valves were opening during unoccupied times and heating the entire building all summer. This happened after a BAS software upgrade and was not noticed. After the problem was corrected, the savings made a 33% swing and were back on track.
LED LIGHTING

LED lighting was used to upgrade the entire facility and reduce maintenance costs. These uplights had a new fixture insert that was also dimmable for maximum versatility and savings.
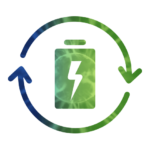
REAL-TIME MONITORING AND CONTROLS
Real-time monitoring and controls spot problems in the BAS and plant operations based on energy usage not just performance. Usage spikes out of the norm indicate equipment or control malfunctions long before they would normally show up on the utility bill. Other issues concerning parts failure are also spotted in advance preventing costly maintenance.
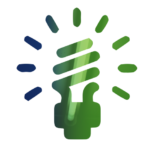
CUSTOM CONTROLS
Tower developed a control strategy that didn’t interfere with the existing oxidizer operation and maintained discharge air pressures through the stack. Safety issues were also integrated for fire and low discharge air temps to prevent the system from cooling in the event of oxidizer shit down or failure. Additional integration allows visibility through the existing new BAS and provided data for temps throughout the plant and heating control of the MUA units. The MUA units were controlled also to maintain slightly negative building pressure in the areas served. This allowed the units to fully take ad- vantage of the MUA provided by the new system and modulate down based on building pressure.
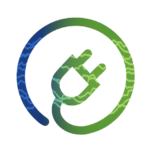
TOWER ENERGY MECHANICAL
Licensed mechanical contractors with 30+ years of experience. Licensed master electricians specializing on controls. Practical customized engineering experience to spot opportunities and estimate payback and costs.