EXISTING CONDITION
Energy costs were spiraling out of control due to uncontrolled building automation. Heating systems and cooling were operating at the same time and with-out central controls.
The center of the plant was all refrigerated which suffered from uncontrolled heating in the adjoining areas. Growth of the plant and change in use led to a variety of conflicts.
BUILDING AUTOMATION WAS ADDED TO ALL HVAC AND VENTILATION
All the RTU’s, unit heaters, exhaust systems, and waste heat was automation with visibility in order to take control of the building as a whole. Aisles adjoining the refrigerated areas were being heated to 68F all year which was affected by the opening and closing of large doors entering the process areas. This process cooling was then affecting the heating stats and causing the heating system to operate.
REFRIGERATION SETPOINTS OVER COMPENSATED
When the refrigeration was not able to make temp the assumption was that the load was too high from production. The problem that was discovered, however, was that the load was artificially created from the adjoining area temps not being controlled. The higher temps also have more humidity which was causing condensation in the refrigerated areas and icing on the evaporator coils. This caused the reaction to not turn off the refrigeration even when in weekend shutdown or during cleaning fearing evaporator icing again. Air curtains were also not functioning which added to the problems.
DE-STRATIFICATION FANS ADDED TO THE CEILING AND AUTOMATION
The high ceilings had no de-stratification fans which were allowing all the heat to float to the ceiling. Fifteen new fans were added and are now controlled by the automation. At 60F in the plant halls, the destratification fans are the first to turn on when there is a call for heat. The plant hall temperatures are set to 55F. Heating systems don’t turn on until 55F but the refrigeration liquid lines above the cooler were also heating up the ceiling. This heat is now circulated down to the aisles.
Electric Saving
DATE | 2018 | 2019 | SAVINGS / MONTH |
---|---|---|---|
11/26/19 | 718,600 | 550,335 | $ 14,194.26 |
12/28/19 | 683,200 | 556,412 | $ 9,908.02 |
1/29/20 | 774,400 | 568,000 | $ 14,471.89 |
THREE MONTH ELECTRIC SAVINGS
$38,574
Your Content Goes Here
HEAT RECOVERY OFF COMPRESSORS USED FOR MUA AND PLANT HEATING
The plant had no dedicated MUA system to balance all the exhaust and all the compressed air heat was being discharged into the plant most of the year since the hall set-point was at 68F and the refrigerated spaces were cooling the halls below that when the doors opened. This added heat was adding to the refrigeration load. New controls were added to only allow the compressor heat into the area when needed.
Therm Saving with Automation
DATE | 2018 | 2019 | % Saved |
---|---|---|---|
10/23/2018 | 17,716 | 12,604 | 29% |
11/25/2018 | 19,539 | 14,556 | 26% |
12/25/2018 | 22,684 | 12,658 | 44% |
Note: Project was starting and savings were accelerated during progress
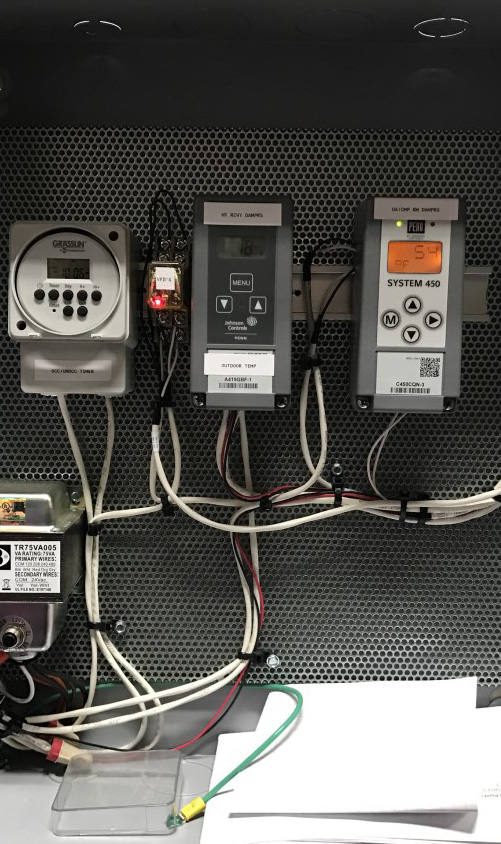
Therms 3 Month Saving
Projected ROI After Grants: Yearly
10 Year Projected Savings
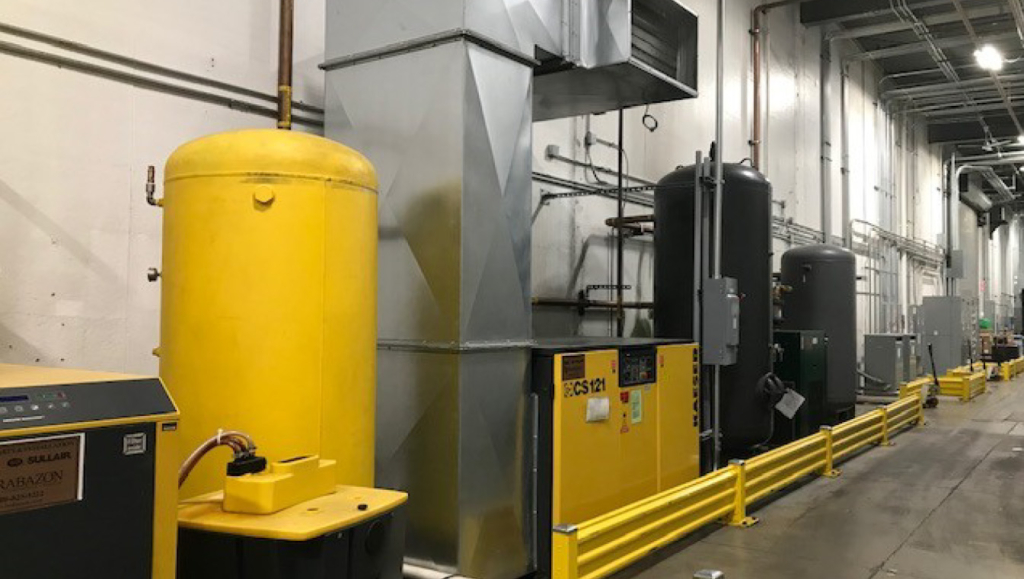
Heat recovery off the 2-50HP compressors was controlled by the new automation to not overheat the aisles next to the refrigerated production. With the lower setpoint and destratification in place the compressor or lights and not almost completely heating the spaces next to the production areas.
Ventilation Controlled
Existing ventilation was running 24/7 and exhaust all the heat off the ceiling all winter. Since the plant operation had changed the exhaust was no longer desired for most of the year. A control was set to only exhaust in summer when temps were over 76 at the ceiling. This also allowed for better heat retention.
Split Heat Pump Added to Office
Conference rooms and side offices were fighting with the main RTU and had no VAV to control temps. The spaces were too cold in winter and too hot in summer. A split heat pump air handler was added to give supplemental control to these areas.
Energy Tax Exemption
The sales tax exemption for energy used in manufacturing was not being taken. Tower calculated and submitted the paperwork for both a 5-year refund and exemption going forward. This substantial refund was then put to use to fund the new energy projects with an additional quick payback. There was also a tax saving on the investment itself since the improvements were deductible 100% in the year accrued.
Automation’s Real Time Data
Modern Automation systems give real-time data and control on how the units are operating. This information is invaluable for troubleshooting and tuning the system for the desired result.
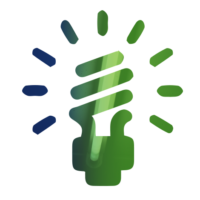
REAL TIME MONITORING AND CONTROLS
Real time monitoring and controls spot problems in the BAS and plant operations based on energy usage not just performance. Usage spikes out of the norm indicate equipment or control malfunctions long before they would normally show up on the utility bill. Other issues concerning parts failure are also spotted in advance preventing costly maintenance.
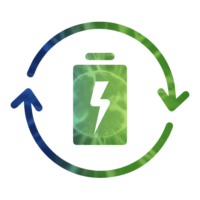
CUSTOM CONTROLS
Tower developed a control strategy that didn’t interfere with the existing oxidizer operation and maintained discharge air pressures through the stack. Safety issues were also integrated for fire and low discharge air temps to prevent the system from cooling in the event of oxidizer shit down or failure. Additional integration allows visibility through the existing new BAS and provided data for temps throughout the plant and heating control of the MUA units. The MUA units were controlled also to maintain slightly negative building pressure in the areas served. This allowed the units to fully take ad- vantage of the MUA provided by the new system and modulate down based on building pressure.

TOWER ENERGY MECHANICAL
Licensed mechanical contractors with 30+ years of experience. Licensed master electricians specializing on controls. Practical customized engineering experience to spot opportunities and estimate payback and costs.