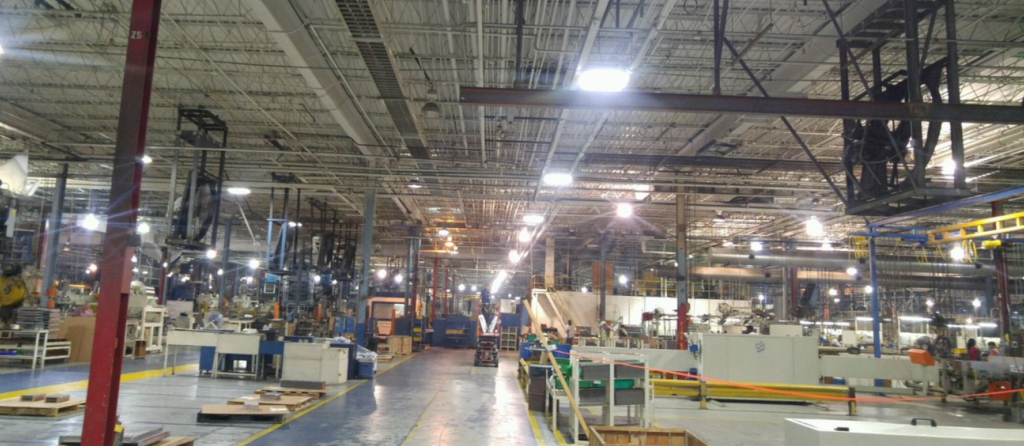
EXISTING CONDITION:
The lighting in these plants was a combination of HID and T8 technology which was inefficient and expensive to maintain. The lighting also was inadequate and needed to be improved.
The compressed air system was in disrepair and had no modern controls to reduce usage. There was also no heat recovery that could be used to heat the facility in the winter.
OVER 1.9 MILLION SQ.FT INSTALLED OVER 4 LOCATIONS
Thousands of fixtures were removed, relocated, and upgraded with plugs and outlets as needed. With the change in use over the years almost 50% of the plant was over lit and the other 50% under lit. Fixtures were moved, raised, lowered, and adjusted as needed to meet the new manufacturing requirements during the installation. Almost five hundred redundant fixtures were removed to save more energy. Some locations saw a 35% reduction in energy use for the entire plant.
Task Lighting Converted
Fixtures over machines used for task were converted to LED while using the old shell and fixture. This lowered installation cost and eliminated the need for shatter guards since the fixtures were not glass. Yellow covers were also eliminated which made the new system twice as bright without adding cost or additional energy.
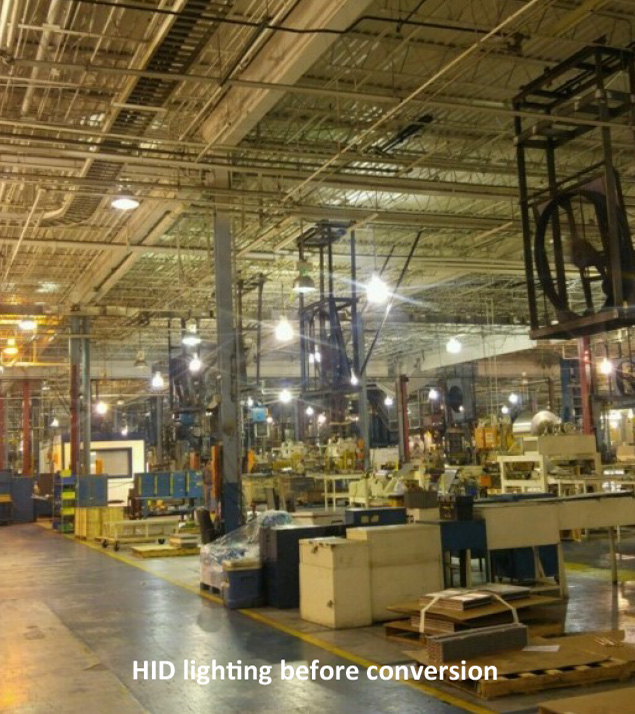
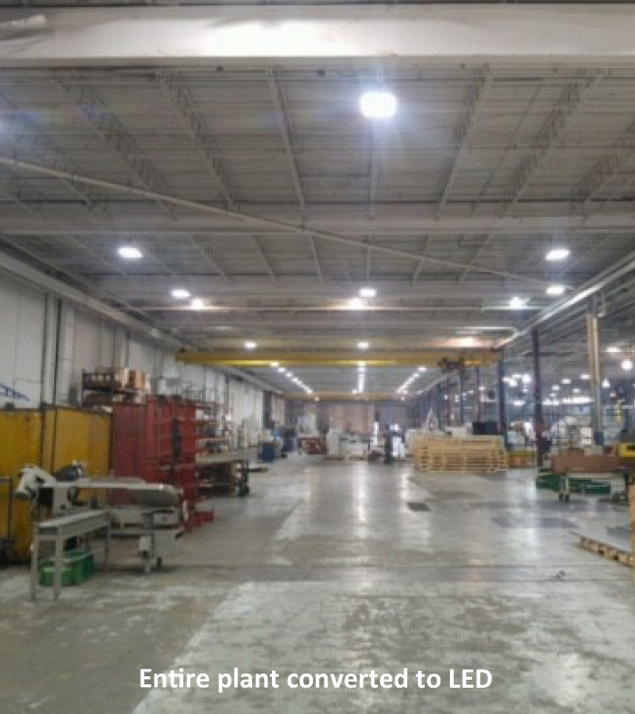
Office Lighting Replaced at OEM
The existing office lighting was designed in the ’50s when offices used manual entry and there were no computer monitors. The fixtures were also yellowed and in poor condition. After the acquisition, an upgrade was implemented to modernize the look and upgrade the lighting to a non-glare computer-friendly appearance. LED flat panels lowered the wattage from 156W to 38W and nearly doubled the output from the deteriorated existing fixtures.
Average Electrical Saving
Unit | Monthly | Yearly |
---|---|---|
Kwh | $60,990 | $8,630 |
Maintenance | $731,887 | $103,567 |
10 Year Savings
$9,774,811
Your Content Goes Here
COMPRESSED AIR UPGRADED AT THE GRENADA LARGEST FACILITY
The plant had over 1000ph of compressed air capacity but was still renting an additional 300hp due to its inefficient operation. Since the plant was just purchased through an acquisition they had no previous control over how the maintenance was handled and what the cost effects were. Tower analyzed the compressed air system and recommended an upgrade to handle plant pressure requirements and cut costs.
Savings from Compressed Air Upgrade
Unit | Yearly Saving | Saving/Month |
---|---|---|
Rent | $96,000 | $8,000.00 |
KWh | $92,000 | $7,600.00 |
Therms | $52,000 | $5,250.00 |
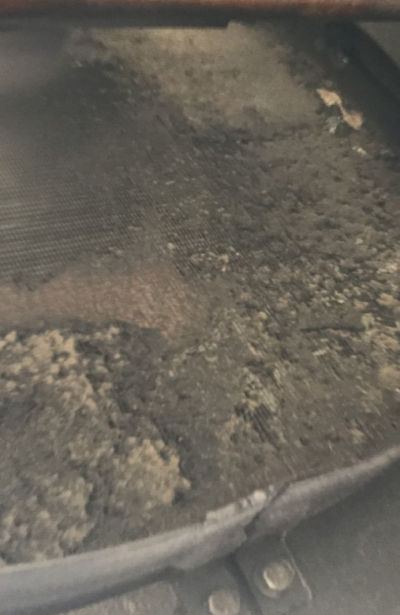
Radiator clogged causing overheating.
Projected Yearly on Compressed Air*
Combined Yearly Saving
Combined Project Yearly ROI
10 Year Projected Saving
*Project was starting and savings were accelerated during progress.
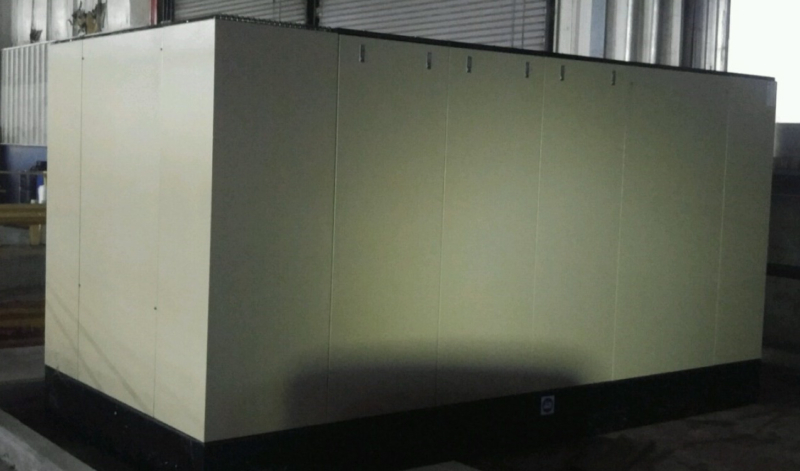
New 300HP VSD compressor was added inside the plant to take advantage of heat available in winter without added expense to facilitate. In summer the warm air is exhausted through open doors and a whole plant ventilation system.
New 300hp VFD Compressor Added
Tower specified a 300HP VFD compressor to modulate the upper load of the plant. The remaining fixed speed compressors were then staged to carry the base load to 100% of capacity, which is very efficient. As the load was not needed, the base line compressors would stage to off, allowing the new compressor again to modulate.
Compressed Air Heat Recovery
The existing system was expelling all the heat to the outside all year. Plant heating, however, even though it was on the south, was substantial due to the size of the plant and relatively loose building envelope. The new compressor was installed inside to take advantage of a simple heat recovery in winter by just expelling the heat above the unit. This will save approx. 83,000 therms throughout the heating season.
Compressed Air Use Efficiency
A plant operational process was looked at for ways to reduce energy with compressed air. Operational startup and shut down procedures were implemented to not have air on when machines were not running. A full-scale leak detection/repair system was also implemented to reduce waste. This cut compressed air requirements close to 150HP.
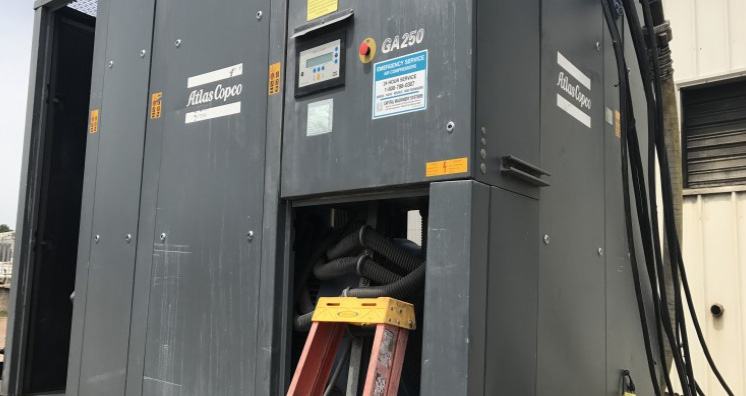
With the existing system running so inefficiently the plant had to rent a compressor at a cost over $8,000.00 per month. The combined savings in energy savings, rental costs, and maintenance paid for the new compressor in one year.
The existing storage system was also in disrepair causing the baseline compressors to run when not needed. These parts were repaired during the process.
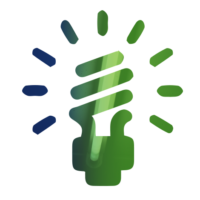
REAL TIME MONITORING AND CONTROLS
Real time monitoring and controls spot problems in the BAS and plant operations based on energy usage not just performance. Usage spikes out of the norm indicate equipment or control malfunctions long before they would normally show up on the utility bill. Other issues concerning parts failure are also spotted in advance preventing costly maintenance.
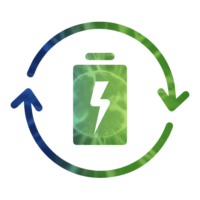
CUSTOM CONTROLS
Tower developed a control strategy that didn’t interfere with the existing oxidizer operation and maintained discharge air pressures through the stack. Safety issues were also integrated for fire and low discharge air temps to prevent the system from cooling in the event of oxidizer shit down or failure. Additional integration allows visibility through the existing new BAS and provided data for temps throughout the plant and heating control of the MUA units. The MUA units were controlled also to maintain slightly negative building pressure in the areas served. This allowed the units to fully take ad- vantage of the MUA provided by the new system and modulate down based on building pressure.

TOWER ENERGY MECHANICAL
Licensed mechanical contractors with 30+ years of experience. Licensed master electricians specializing on controls. Practical customized engineering experience to spot opportunities and estimate payback and costs.